What Is FRP?
Fiberglass Reinforced Plastic (FRP) is an engineered material consisting of reinforcement fibers, polyester resin and additives to achieve the desired performance properties. This combination creates an extremely strong and durable material that can be used for parts inside equipment up to large, heavily loaded civil infrastructure. The type of reinforcement fiber is chosen based on the requirements of the application. For example, carbon fiber is commonly used in airplanes and recreational equipment, while the most common reinforcement material is fiberglass given its combination of properties and cost.
Why FRP is an ideal choice for a wide range of products and offerings:
- Lightweight material. FRP components are extremely lightweight compared to other construction materials. This makes them safer, easier to work and cheaper to transport. They also don't require as much equipment to install.
- Corrosion resistance and low maintenance. FRP is extremely durable, making it suitable for heavy-duty usage in a wide range of environments. Its corrosion resistance makes FRP capable of withstanding salt, water, chemicals and other harsh weather conditions without deterioration. This means it can last for up 100 years with very little need for maintenance or rebuilds.
- Cost-effective. Conserva Composite builds our high-quality FRP components to offer long-term cost savings and profitability through its many beneficial qualities. FRP often offers lower acquisition costs compared to traditional materials.
- Flexible design. FRP is engineered to meet the exact application requirements. Factors such as size, shape, color and functional features can be customized to ensure smooth and easy installation.
- Shorter production and installation time. FRP is prefabricated, allowing crews to install each part much faster. This makes FRP ideal for construction projects in public areas that have tight timelines and limited construction hours.

Benefits of FRP Over Traditional Materials
FRP provides many benefits over traditional materials such as steel, aluminum and wood.
FRP vs Steel
FRP is highly corrosion-resistant, whereas steel is susceptible to rust from chemicals and weather exposure. FRP is as strong as steel and weighs significantly less for a great strength-to-weight ratio. Other benefits that FRP has over steel include:
- Non conductive and impact resistant
- Easy fabrication without the need for cutting torches and welders
- More flexibility in terms of color options and functional features
FRP vs Aluminum
Unlike aluminum, FRP has low thermal conductivity, meaning it serves as a great insulator. It’s also corrosion-resistant, non-conductive and won’t deform under impact.
FRP vs Wood
Wood components are prone to warping, decay and rot. FRP exhibits excellent resistance to corrosion, mildew, mold and other conditions that timber cannot stand up against. FRP can also deliver extreme durability without the need for environmentally hazardous coatings.
FRP vs Concrete
FRP panels are less than 15% the weight of concrete. There is no spalling, cracking or damage from moisture, salt or chemical.
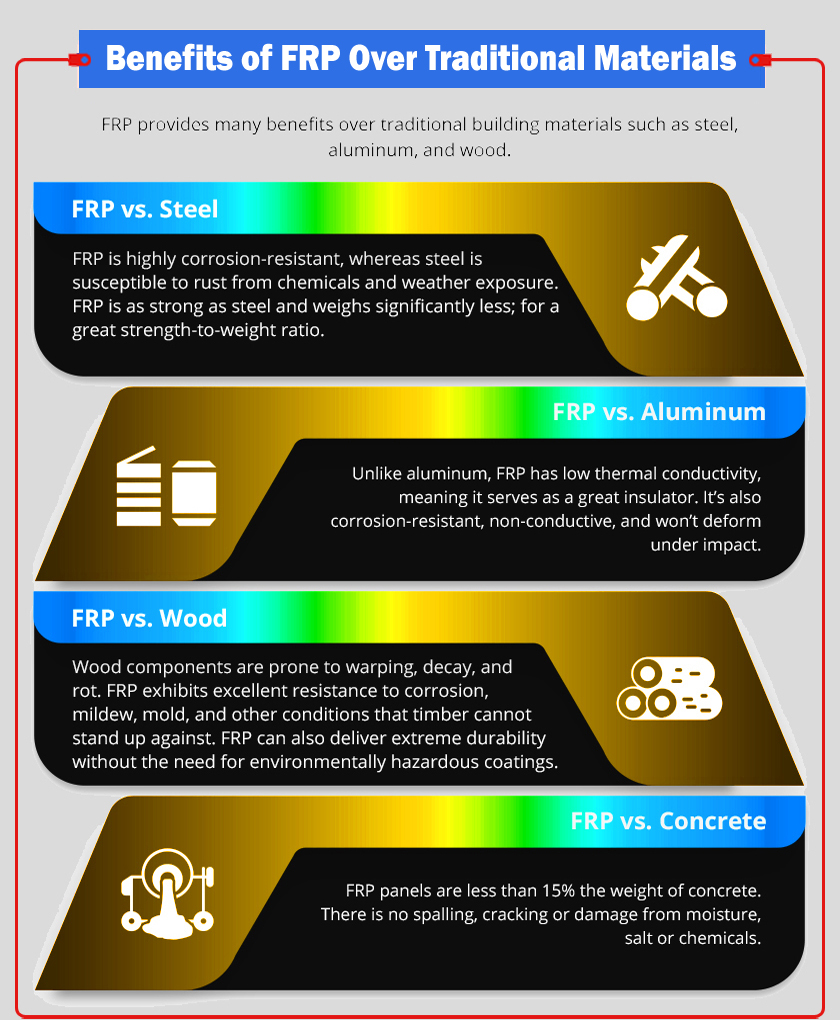
Advantages of Fibreglass Reinforced Plastic (FRP/GRP) Tanks & Equipments
The benefits of using Fibreglass as the material of choice are many. Some of the key benefits are listed below.
1. 100% Watertight
Fibreglass Reinforced Plastic (FRP) tanks are manufactured as a completely sealed unit. Penetrations through the walls are made in the factory with compatible materials. There are no joints in the unit which are required to be sealed on site. This makes the tanks 100% watertight.
Being watertight has two distinct advantages. First, it prevents the ingress of other fluids and gases into the tank. There by avoiding contamination or dilution of the stored product. Second, it prevents the contamination of the surrounding area with chemicals leaking out of the storage tank.
2. Resistance to Chemical Attack
Fibreglass (FRP) was recognised early in its development as having a high resistance to chemical attack. Conserva Composite carefully selects the most appropriate resin system for the required applications to ensure it meets the asset owners expectations.
3. Corrosion Resistance
A distinct advantage of FRP tank is its corrosion resistant to harsh corrosive chemicals and conditions. All FRP tanks are manufactured with high surface corrosion resistance, which is achieved by adding a smooth resin-rich layer which reduces friction. Our FRP tanks guarantee resistance to corrosive chemicals found in sewers and wastewater, unlike concrete tanks. Our tanks have been proven to last in the ever-changing environment and are even built to withstand hydraulic pressure.
4. Low Maintenance
Due to the smoothness of the glass resin interior surface of the Fibreglass Reinforced Plastic (FRP) units, particles have difficulty adhering to the sides. The smooth walls of the Fibreglass Reinforced Plastic (FRP) station mean the time taken and frequency of washing down the tanks and build-up of product on the tank walls is significantly reduced.
Thereby reducing the operator’s maintenance costs and equipment downtime.
5. Quality Control
As part of Conserva Composite quality control system, its FRP products are designed and certified by a practising Composite Materials Engineer to be suitable for the proposed application.
The Fibreglass Reinforced Plastic (FRP) Chemical Tanks are manufactured as complete units under controlled conditions in a factory. Prior to the commencement of manufacture of any FRP components, project specific working drawings are produced for the item. During the drafting process dimensions and clearances are checked to ensure the tank will perform as designed.
As the units are customized for each project these drawings include all the necessary details for their manufacture.
The drawings are submitted to the client for approval prior to manufacture. As part of the Quality Control process the Fibreglass Reinforced Plastic (FRP) units are checked at the various stages of manufacture for compliance with the working drawings.
Our tanks can be constructed in many configurations and are designed and constructed to AS2634-1983, BS4994-1987 and ASME RTP-1 – 2011.
6. Installation
The Fibreglass Reinforced Plastic (FRP) units are supplied to the site complete, with the only requirements being the external connection of pipework and electrical connections. We believe this avoids many potential safety hazards of site fit out.
WHS legislation makes all persons involved on the project responsible for site safety, not only those undertaking the work but those supervising and designing it. By reducing the potential need for hazardous work on site, the use of Fibreglass Reinforced Plastic (FRP) units is actively encouraging a safer working environment and compliance with statutory requirements.
7. Ease of modifications during the life of the tank
During the life of any tank minor modifications are generally required to the external fixtures in the tank. For example, the addition of extra brackets etc.,
These can easily be added to the station by utilising Fibreglass Reinforced Plastic (FRP) brackets or mounting plates which are “glassed” onto the internal walls at the required location. It is not necessary to drill through the wall for anchorage.
As such the overall structural integrity and water tightness of the structure are not compromised.
8. Abrasion Resistance
The Fibreglass Reinforced Plastic (FRP) tanks are manufactured to have high surface abrasion resistance. This is achieved by forming a layer of pure resin material at the surface which is not only smooth, thereby reducing friction, but also has high strength.
9. Customisation
Conserva Composite manufacture products which are customised to an individual client’s requirements. Nozzle size, material types and layout are flexible.
Within engineering limits this gives the designer the freedom to specify the tank layout which maximises operation efficiencies, complies with system parameters and suits the end user’s operation and maintenance procedures.